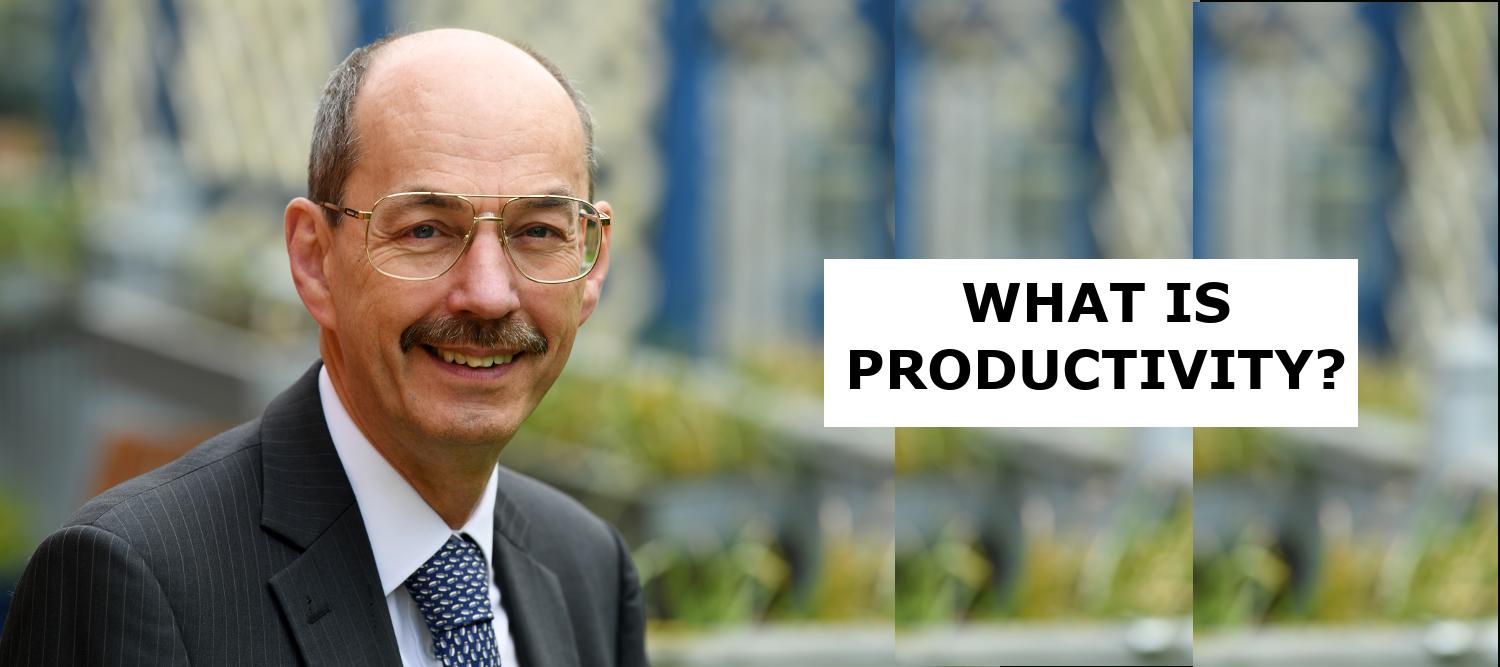
What is Productivity and Why Productivity is Important
What is Productivity requires a definition of Productivity.
By understanding what Productivity represents it allows the positioning of the importance of Productivity for a business.
WHAT IS PRODUCTIVITY
The definition of Productivity is Output divided by Input. It is a number for the ratio.
Although this starts as a simple ratio the calculation becomes quite detailed once the scope of the analysis is determined.
WHY PRODUCTIVITY IS IMPORTANT
Productivity can seem like a Dull calculation and in some respects it is just a number.
The reason that Productivity is important is that allows comparison between teams and between businesses.
For comparisons to most effective them need to be on a similar basis, hence comparisons between competitive businesses operating in the same industry can have real value whereas comparing the business of a Premier League football club with a car manufacturer or an accountancy practice or a hair dressing business are largely only for academic purposes.
Comparison by country demonstrates the relative economic position. It indicates that United Kingdom productivity is slightly lower than the Euro Area average.
A simple view of this analysis can miss the fact that different countries have different mixes of industries, which impact the overall figures.
When considering productivity within car manufacturing businesses, companies such as Toyota, Ford, Volkswagon, Nissan, Honda, etc. can all be ranked. There are many similarities in that they all produce cars on a global scale. However, the productivity of similar plants operating the same country can be quite different.
When performing such comparisons using productivity it is clear that there are many factors which need to be recognised.
The better the Productivity of a business, the stronger it is financially and therefore it most likely to be able to succeed against its competitors.
As Productivity changes measure the performance of a business, any increase in productivity means that is more profit for a company. It is this relationship which drives the discussion about how much staff in a business should be paid. If they are more productive, there is more money available to pay staff.
WHAT ABOUT INDIVIDUAL PRODUCTIVITY / PERSONAL PRODUCTIVITY?
Every person needs to take some responsibility for their own productivity.
Much has been written about methods, techniques and tips for ways to work productively. Advice usually involves staying focussed, working on one task at a time. It is generally accepted that distractions reduce productivity, hence working on a task without interruptions will produce the best results. As humans we can only concentrate for limited periods of time, therefore theories exist about structuring activity to have periods of concentration and well defined breaks.
There is a famous quote
“Productivity Is About Your Systems, Not Your People”
by Daniel Markovitz. This can put issues concerning personal productivity in perspective.
WHAT ABOUT TEAM PRODUCTIVITY?
A highly motivated team that has good cohesion is expected to perform well in sport. Many gurus have proposed attitudes and approaches from the sporting world as means to achieve good performance in business situations. There many successful case studies where team productivity has been enhanced through the application of such methods.
The big difference between sports teams and business situations, is sports teams compete once every few days for a small number of hours. Business teams have to operate many hours day and typically 5 days a week (ignore shift work in this context). It is this extended activity which makes it difficult for many methods to work, as they improve productivity but only in the short term. There tends to be a gradual fade in productivity levels even for sports teams.
According to business advisor Peter Drucker:
“The productivity of work is not the responsibility of the worker but of the Manager.”
This demonstrates the responsibility for Team Productivity.
ARE THE JAPANESE LEADERS IN PRODUCTIVITY?
There are many Japanese terms associated with productivity. Terms such as Jidoka, Heijunka, Kaban, Kaizen, Muda elimination and Poka-Yoke. These are explained on the Productivity FAQ. There are also working methods that have become associated with Japanese car manufacture activity such as “Just In Time” and “Total Productive Maintenance”.
The Japanese car manufacturers have been successful businesses that have grown to operate on a global scale and no doubt part of that is due to their approach to productivity.
The OECD chart shown above that overall Japan is not a leader in productivity.
HOW TO IMPROVE PRODUCTIVITY
With an understanding of what Productivity is and why it is important, questions rapidly move to how to improve productivity.
To consider ways to improve productivity it is essential to look at different elements that can determine differences in production. The elements will vary between businesses but usually include:
- Capital – investments in plant, machinery, equipment, land, premises
- Work organisation – Process completeness, Process flow
- Quality – Fit for purpose, Defects, Repairs, Warranties
- Staff – Knowledge, Training, Skills
- Materials – Specification, Supplier Tolerances, Variances
To improve productivity there needs to be some form of change and potentially an investment. Before making any change, a base line for the measurement of productivity needs to be created. This does need to a highly complex calculation with a high level of precision because the emphasis is on change that improves productivity. This means that a broad assumption can be used that everything will continue as normal, apart from the element in the processing which is going to impact productivity.
For example, if a change is made to the material that is an input to the process by purchasing it from a supplier who delivers to the specification but with less tolerances in the measurements, this could result in a lower number of defects during manufacturing and a reduction in the repairs required as well a smaller number of warranty claims. Such an improvement in quality will improve productivity.
Another example would be where a capital investment is made in automation, this could reduce staff effort required and improve consistency of the output. The improvement in productivity that will result from such an investment will be achieved provided that the savings are greater than the cost. Accountants can determine the right factors to handle capital, depreciation, etc.
THE ON-GOING IMPORTANCE OF PRODUCTIVITY
With the understanding that Productivity is important, it becomes an on-going challenge to improve productivity. A one-off change to improve productivity will help a business but it effectively establishes a new base line from which further improvements need to be made to get accumulated changes in productivity that compound the benefits.
With productivity levels being a factor in business competitiveness, it is expected that once a advantage is gain, the competitor businesses will respond with their own changes in order to reduce the effectiveness of productivity difference.
The need for continuous improvement is an essential element of “Lean manufacturing” and there is a similar need for on-going improvement in productivity. Much has been written on the “1% continual improvements” approach adopted by British Cycling and it is a good strategy for business to seek margin productivity improvements all of the time. Such changes in productivity compound and are typically associated with less risk to the business process each time they are implemented.
MEASUREMENT OF PRODUCTIVITY TO TRACK IMPROVEMENTS
To be able to detect improvements in productivity it is necessary to be able to have a measure of productivity. With the emphasis placed on change in productivity, measurements need to be accurate enough to detect the impact but to be most useful they can be expressed in terms of “Output Units” rather than fully costed monetary values.
For example, if the team productivity that is being measured produces “Widgets”, counting the number of “Widgets” produced each day by the team makes a quantifiable measure that is understandable and relevant. The monetary value of the “Widget” is not the concern. This can also avoid the “Fractional” debates about the value of “Half a Widget”. Many changes that are made to improve productivity will impact outputs in a number of ways, e.g. quality, but keeping measurement to discrete output units will allow small variances in the assumptions used for valid comparisons to be made.